Is your supply chain ready for the COVID-19 shock?
No time? Grab the information and go
Here's what you need to know in short:
As COVID-19 spreads, supply chain disruption is expected globally. It will fast become a major stress-test of virtually every firm’s supply chain and will expose weaknesses. Gaining a detailed understanding of the risks, complexities and exposure for an organisation by ‘peeling the operational onion’ is imperative. By taking immediate actions to improve the readiness and resilience of their supply chain, it will help organisations to effectively navigate the rapidly changing dynamics of a connected world.
As COVID-19 spreads, supply chain disruption is expected globally. It will fast become a major stress-test of virtually every firm’s supply chain and will expose weaknesses. Gaining a detailed understanding of the risks, complexities and exposure for an organisation by ‘peeling the operational onion’ is imperative. By taking immediate actions to improve the readiness and resilience of their supply chain, it will help organisations to effectively navigate the rapidly changing dynamics of a connected world.
What can I do immediately?
There are four broad activities that every company needs to address:
1. Form a crisis team
This is the time for a ‘whole-of-company’ response – there is no time for silos. Pull together a multi-functional team of a-players, reporting directly to the c-level. This is a high-speed, agile and iterative process – analyse, plan, execute, and start again. Key steps you can take:
- Create a high-level, multi-functional team and assign accountabilities and roles: Establish, objectives, policies and guidelines, meeting cadence and reporting principles (e.g. transparency).
- Set up a crisis centre (Mission Control room) and get key stakeholders involved
- If time permits, run simulation and planning exercises that are the most effective for your situation. Some may be done in parallel while others can be split for different product categories (e.g. strategic items vs. commodity items):
- Desk check: Validate plans and procedures and any changes to them with key owners.
- Tabletop exercise or Command Post Exercise: This covers all aspects of crisis management. All participants receive the same information about the simulated crisis and their role in advance. They then play it out and document discussions and learnings. The Crisis team deals with questions and solutions like a realistic and evolving scenario.
- Red team/blue team: In this exercise, the red team creates scenarios or important business disruptions and the blue team tries to develop a solution to address the problems. This type of exercise generates problems and solutions that are normally outside-the-box thinking.
- Enact short-interval reporting to get information flowing, monitoring for any changes to the situation and to coordinate rapid internal and external communications. Provide the C-level support to knock down obstacles.
2. Peel the ‘onion’
Every firm needs to understand both exposure and risk to get ahead of this rapidly unfolding crisis. Most supply chains are multi-layered with both risk and potential opportunities below every layer. For virtually every critical supplier and component, the supply chain needs to be understood to the source.
While some companies have a good understanding of how their first-tier suppliers will be affected, it is important to examine risks further into the supply chain. Key activities should include: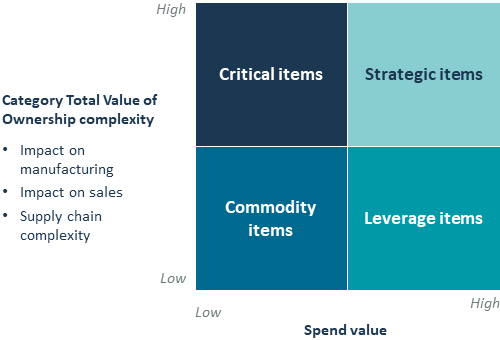
- Reviewing and revising existing business continuity plans including insurance
- Reviewing key metrics (e.g. cash flow, inventorylevels and buffers, revised demand forecasts, etc.) and determining the urgency of response required
- Prioritising the critical items first, followed by strategic and leverage items (in the current situation, commodity items may also be in short supply and should not be ignored)
- Determining ultimate sources of goods/services by country/ region, not ignoring complex domestic supply chains
- Developing a 3-6-month requirement forecast and determining how many weeks of materials are in the supply chain pipeline internally and at first-tier suppliers
- Understanding the current state of inbound and outbound logistics supply chains (driver shortages may impact the availability of domestic transportation)
- Conducting scenario planning through the crisis management recommendations listed above to understand the impact of prolonged shutdowns and shortages, both with internal production and distribution sites as well as external suppliers
3. Execute the plan
Rapidly execute remedial plans for at-risk items. Aim for concurrent activity in analysis, planning and execution to tighten the time cycle. This is a collaborative process with suppliers and customers characterised by frequent, frank and supportive communications. It is also important to adopt an agile approach and constantly revisit these plans given the rapidly evolving nature of the crisis. Organisations should:
- Plan how to be your existing supplier’s ‘best customer’ to avoid being put on allocation or low priority by:
- Concluding outstanding supply agreements and get critical items under contract
- Sharing requirement forecasts with suppliers
- Making selective forward buys to include physical delivery or pre-purchased materials held at the supplier’s location
- Paying outstanding balances to prevent supplier credit holds and consider selective early pay programmes
- Identify alternate suppliers, countries, and products – use digital tools that enable you to identify sources and take action quickly
- Review opportunities for reshoring or leveraging closer sources
- Understand the risk and timing of supplier changes including regulatory testing and certification and availability and timing of back-up or new tooling
- Determine options to address freight issues
- Develop processes for monitoring the financial health of critical suppliers
- Execute, measure results, and re-plan
4. Build resilience
As remedial plans are put in place, capture learnings and codify processes and tools used. Over the longer term, firms need to make their high-urgency response to the impending COVID-19 crisis part of their typical business process and develop procedures and ‘Wiring’1 to support this level of supply chain analysis, insight, and action. Consider implementing the following:
- Review and determine optimal cost/inventory-level tradeoffs and supplier/country concentration levels for critical and strategic items
- Identify alternate sources of supply for other key at-risk product groups or regions
- Establish a supplier management process for strategic suppliers:
- Revise Key Performance Indicators to include learnings from Crisis team analysis and short-term plans (e.g. supplier countries and levels of concentration)
- Establish a consistent performance review cadence
- Implement joint improvement opportunities - improve forecasting and demand planning and consider helping suppliers strengthen their supply chains
- Establish ongoing customer stakeholder reviews to tightly integrate business requirements and supply chain design
- Establish and formalise a Standard Operating Procedure for supply chain disasters
Conclusion
As COVID-19 is now a global pandemic, it will continue to dynamically impact global supply chains in uncertain ways. There will be no safe regions and it will be impossible to predict what will be impacted next. We understand how difficult these times can be, but taking immediate steps to improve the readiness and resilience of your supply chain will help you navigate the rapidly changing circumstances of a connected world.
Download this article
Reach out to our supply-chain and procurement experts to find out how we can help you de-risk